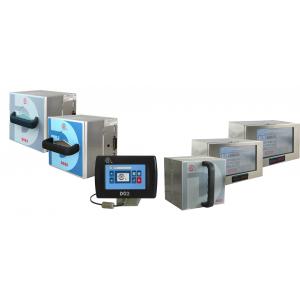
Add to Cart
TTO PRINTER Intermittent Continuous TTO Coder/TTO Date Printer For Flow Packing Machine
DIKAI D03S Thermal Transfer Overprinter (TTO)
Compared to traditional contact coders such as hot-stamp or roller coders, thermal transfer overprinting offers superior print quality and lower costs.
From label overprinting, to high speed digital coding on vertical bagging machines with flexible packaging, the Dikai thermal transfer printer is able to deliver fast print speeds, minimising downtime and ensuring the lowest possible cost of ownership.
Quick Details
Dikai TTO coders use thermal printheads paired with thermal transfer ribbon to apply a consistent and reliable mark on your products. The D03S and D05S models offer high speed printing of incredible looking variable text, serial numbers, barcodes, and graphics at a razor-sharp 300 DPI.
Most people in life will look at the production date information when shopping in the mall, and they will also notice that the supermarkets are also soft-packed foods, some of which are ambiguous and others are clearly visible. In fact, apart from the erosion of packaging date by refrigerator air conditioning, the main reason is that they chose different coders.
Coding machines are roughly divided into bar code coding machines, TTO thermal transfer coding machines, thermal foaming coding machines, etc. However, the platinum high logo thermal transfer printer under ITW Group of the United States is the most widely used in the flexible packaging industry, which has a high ratio of letter to price and has been well received by many users!
The ribbon thermal transfer printer, also known as tto, uses ribbons as consumables. TTO ribbons have a wide range of widths, which are pasted between 33 mm and 55 mm respectively, which optimizes the utilization ratio of ribbons. Professional technology and imported raw materials provide high-quality products and services to more than 500 large and medium-sized customers in China.
Tto thermal transfer printer has reliable structural design and professional technology, including direct ribbon drive and improved ribbon box design without wearing parts, and does not need preventive maintenance inspection at all. Each print head has a row of heating elements, and the heat generated by these elements melts the ink. At the same time, the ink is transferred to the substrate by air pressure to realize printing. Its advantages are easy coloring, difficult erasing of printed contents, uniform and clear printing, and suitability for various packages.
Application:
* Horizontal Continuous packaging machine
* Vertical Intermittent packaging machine
* Labeling Machine
* Feeder
Technical Details:
Specification | |
---|---|
Print Head | Kyocera, 32mm; 300DPI |
Print Area | Intermittent: 32mm*60mm Continuous: 32mm*100mm |
Ribbon Size | 33mm*500mI |
Printing Frequency | Intermittent: up tp 350PPM Continuous: up to 40 meters/ minute |
Environmental Operation Temperature | 0-40℃ |
Relative Humidity | 10%~95% (non-condensing) |
Power | AC110~220V, 50/60Hz, 150W |
Air Supply | 6bar/ 90PSI(MAX) dry uncontaminated |
Weight | Print head: 8.5kg, Control box: 2.0kg |
Dimension(L*W*H) | Print Unit: 188mm*190mm*180mm Controller Box: 210mm*180mm*155mm |